IIoT as a foundation for the smart factory
Modern industrial companies are fortunate to run in a time of great opportunities created by smart technologies and devices. The Industrial Internet of Things (IIoT) allows transforming vast amounts of data collected from such devices into valuable knowledge and insights, which help increase operational efficiency and uptime, boost productivity and reduce costs significantly.
In this article, we will talk about the compelling benefits of IIoT for industrial companies and the requirements to sensors, edge devices, machines, and other elements designed to fit with the innovative IIoT environment.
What is IIoT?
The Industrial Internet of Things (Industrial IoT, or simply IIoT) refers to collecting and analyzing data from interconnected objects in order to enable equipment monitoring and production tracking. The definition “industrial” indicates that this concept is realized in the industrial environment, such as manufacturing, transportation, construction, gas and oil, energy, and even aviation.
Physical machines equipped with sensors and edge devices aggregate the information and send it to control units (cloud network) for further analysis and investigation. This helps visualize and create an accurate picture of all operational processes and equipment state-of-health in real-time. The results of data analysis not only allow engineers and managers to detect productivity bottlenecks, but also predict arising problems and take all required measures for preventing unplanned downtime.
IIoT enables industrial companies to build highly complex smart systems by interconnecting billions of devices at once. The extent of this capability is easy to represent using the following ratio: the number of things that can be connected to the Internet already exceeds 50 billion, while the overall population on the Earth is about 7.6 billion.
IIoT-connected sensors can be implemented at every level of factory infrastructure to get as much actionable data as possible, which in turn, becomes a key driver for processes optimization and transformational business outcomes. All this creates a strong foundation for the Smart Factory (also known as the Smart Manufacturing). Although this concept is worth a separate topic of discussion, a few words about the Smart Factory must be said to better understand what we are talking about.
The Smart Factory as a term is usually defined as an intelligent and agile system (network of systems) that connects all physical and digital components of the production technology chain within a factory (manufacturing plant) to enable them to run autonomously, solely under human supervision. Such multilevel interconnection and automation enable easy control of every manufacturing process to be safe and effective, as well as allows fast adaptation to extraordinary situations. The Smart Factory comes with much more definitions out there, but all of them underline the same key elements: intelligent assets, connectivity, network communication infrastructure, cloud-based data management, and automation.
Compelling benefits of IIoT for industrial companies
While defining IIoT, we have already mentioned a number of key benefits. The usage of intelligent assets at factories and plants contributes to productivity and process management enormously. Every manufacturing flow can be reviewed from another perspective, analyzed, rethought, and optimized based on detailed and verified analytics. Engineers, operators, managers can easily identify and reduce untapped production resources, thus increasing revenues and opening up new opportunities for growth.
The list of IIoT drivers is extended, but we tried to focus on the most principle here:
- Enhanced operational efficiency
- Increased productivity and minimized waste
- Reduced downtime and costs
The first three benefits are grounded by the same factor. The accurate and complete data received from sensors and edge devices allows operators and engineers to timely detect improper behavior in the processes and prevent equipment failures (preventive maintenance instead of time-consuming repairs). This enables them to upgrade the existing processes and equipment rather than invest efforts, time and money to additional digital and physical resources. Moreover, tracking spare parts and materials significantly facilitates supply management, which also contributes to enhancing efficiency and uptime.
- Reduced gaps between planned and actual production terms
Optimized production processes, increased uptime and proper management help finish production without delays.
- Improved final product quality
Reducing downtime and maintenance costs allows concentrating on more sophisticated issues, such as implementing innovations and improving the product itself. This looks even more feasible, since automated and controllable processes minimize the risks of human errors.
- Increased machines and assets implementation
Real-time monitoring of equipment state-of-health and performance allows preventing failures before they occur. Sensors can also provide information about some environmental conditions (temperature, humidity) that can negatively affect the equipment functionality and reduce its lifetime. The simplified predictive maintenance approach will encourage industrial companies to increase the number of machines and assets to scale productivity without extra costs for repairs and related issues.
- User-friendly interfaces
The personnel are no longer required to be IT experts to coordinate the process. Comprehensive and intuitive widgets enable operators to learn tools quickly.
- Centralized database
Due to intelligent data collection and management, it’s possible to organize a common data and knowledge base across a factory.
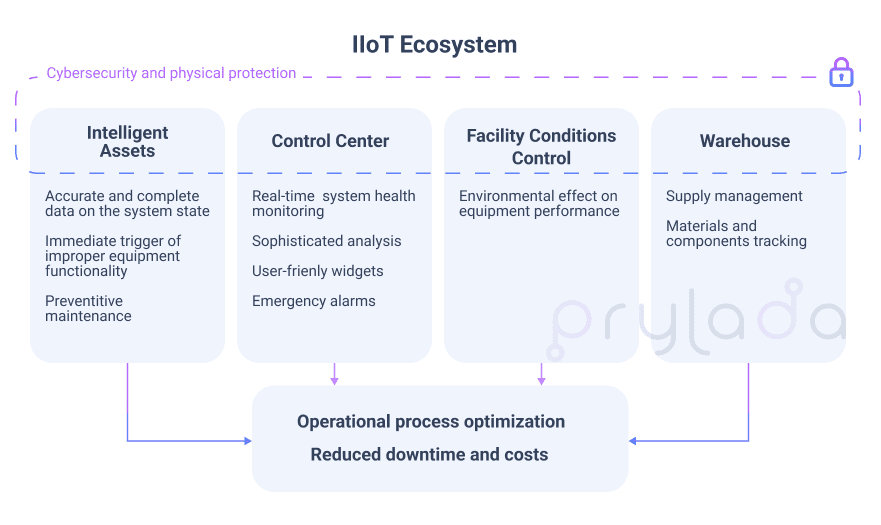
Requirements and barriers on the way to IIoT-driven factory
Definitely, the benefits provided by IIoT are more than attractive, that’s why more and more companies are showing an increasing interest in smart technologies and start deploying them at their factories. But for some companies, the IIoT adoption may turn into a heavy lift, since their current systems are not able to overcome barriers created by the overwhelming volume, variety and velocity of industrial data sets.
Industrial data is extremely complicated due to the following factors:
- Massive volumes
- Different source types and formats
- Complex data relations
- Different sizes
- Messy data
- Varied frequency
Extracting business values and insights from such complex data sets requires new sophisticated data systems. The success of analysis depends on the accuracy and completeness of aggregated data, that’s why sensors must be highly sensitive and intelligent. Other requirements to systems and equipment arise from the challenges that industrial companies face during their transformation into smart facilities.
Morgan Stanley in the Automation World Industrial Automation Survey identified nine categories of blockers to IIoT adoption and specified challenge percentage for each category.
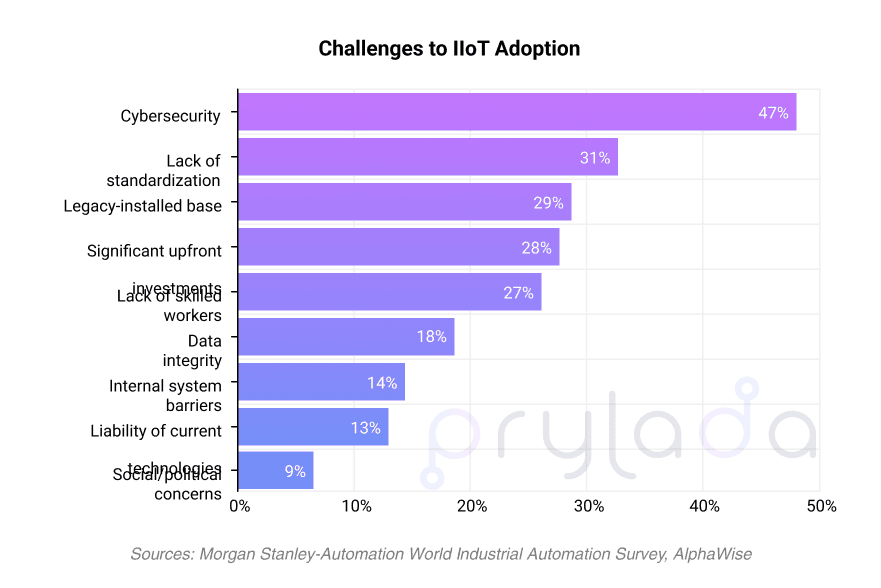
Cybersecurity and privacy protection
Cybersecurity and privacy protection take the first place among other IIoT challenges. With the global scalability and connectivity of modern systems, industrial companies must protect all sensitive data from potential vulnerabilities and cyberattacks.
Standardization
The primary purpose of standardization is to ensure interoperability between various components of the IIoT ecosystem. Problems arise when new services and technologies are designed to comply with the standards other than those the existing systems meet, or lack standardization at all. Moreover, different elements of the existing systems may not be compatible with each other from the very beginning. That’s why one of the basic requirements to the IIoT-driven factories is enabled communication between all machines, regardless of the communication protocol, operating system platform and connectivity standards.
Objects Identification
To ensure easy integration of physical and digital objects into a single IIoT infrastructure, it’s essential to figure out a transparent and comprehensive method of naming and identifying such objects and services across the system.
Skilled Workers
Data is the key element of any IIoT-driven system. However, simply aggregating data is only half the success. An increasing number of objects connected to the system generates a huge and messy information steam, which is extremely confusing rather than helpful. Defining an effective method of analysis and extracting business value from such data requires extended expertise and proficiency from the personnel, which may become a real problem for many end-users.
Seamless IIoT adoption with Prylada
Even though some of the encountered challenges may seem insurmountable at first glance, the implementation of IIoT technologies is becoming more and more feasible and affordable with innovative solutions constantly appearing to serve this purpose.
Designed to meet the existing requirements and fit with various deployment cases, the Prylada Gateway represents a complex out-of-the-box solution for IIoT adoption, from sensors to customized software. Such a modular approach along with the backward compatibility facilitates the integration process and makes it adjustable.
One of the key advantages of the Prylada Gateway is a high level of security, which is achieved by applying the latest world standards in this area, such as SSL/TLS Certificates, JWT, Encrypted Storage, etc. Prylada supports a variety of globally recognized authentication protocols, methods and standards, for example, OpenID, SSO, MFA. FIM, etc. All this makes communication between factory platforms and any third-party system devices (endpoints) as secure as it’s possible. Moreover, all data are stored in an encrypted way inside a trusted storage.
Another factor facilitating IIoT adoption is Identity and Access Management (or simply IAM). IAM is about defining and managing the roles and access privileges of individual network entities (users and devices). Prylada provides different options of user authentication (OpenID Connect, Social Networks) and an additional multi-factor authentication (MFA) layer. This ensures easy connection of new users and systems, as well as enables access roles configuration. To get more details about the Prylada Gateway in terms of IIoT adoption, email us at contact@prylada.com.