Pump vibration monitoring at PCB manufacturing
Introduction
Printed circuit boards (PCB) are widely used in household appliances, communication equipment, computer engineering, and automation systems. Electronic devices based on PCB are also successfully used in the medical sphere, automotive industry, and other areas of industrial electronics, such as aviation, shipbuilding, and aerospace.
The production lines operate 24/7. Periodic maintenance with a full stop of a line is planned and scheduled months in advance. In case some of the essential equipment fails during the manufacturing process, the whole production line stops running, and the manufacturer suffers heavy financial losses.
01
Challenge
A special difficulty and responsibility of the task were represented by the importance of the pump role in the technological process. A pump malfunction caused violation of the production technology, and the whole batch of the produced PCBs was disposed as defective.
When a malfunction occurred, the internal parts of the pump started hitting each other, thus causing their destruction and abnormal vibration. So the increased level of vibration was considered as the primary indicator of the pump breakdown.
The customer also remarked high importance of visual consistency of the control results. Vibration reports should have been presented in the form of charts, the way they had been maintained previously. That approach would allow the customer to avoid interrupting the operational processes and retraining the personnel.
02
Why the client chose our vibration monitoring system
On-premises deployment option
Short timeframe
Reasonable price
Out-of-the-box solution
Hardware and software customization
03
Solution
To implement the concept, the Prylada team designed a new type of extension board, which allowed connecting the customer’s sensors to the Prylada gateway. The development of extension board took no longer than 4 weeks. At that, one gateway could be equipped with 8 expansion boards to provide 56 inputs for similar sensors.
%20(2).webp)
First, the Probeberry gateway aggregates accurate vibration data from the sensors embedded with the pumps.
Later, the aggregated data is transported via Ethernet to the Prylada on-premises server, which runs in the customer’s local network.
Prylada also provides a user interface to display the vibration data in an intuitive dashboard.
Another month the team dedicated to assembling the components into a single solution and making the necessary configuration. The suggested operating principle was based on several consecutive steps.
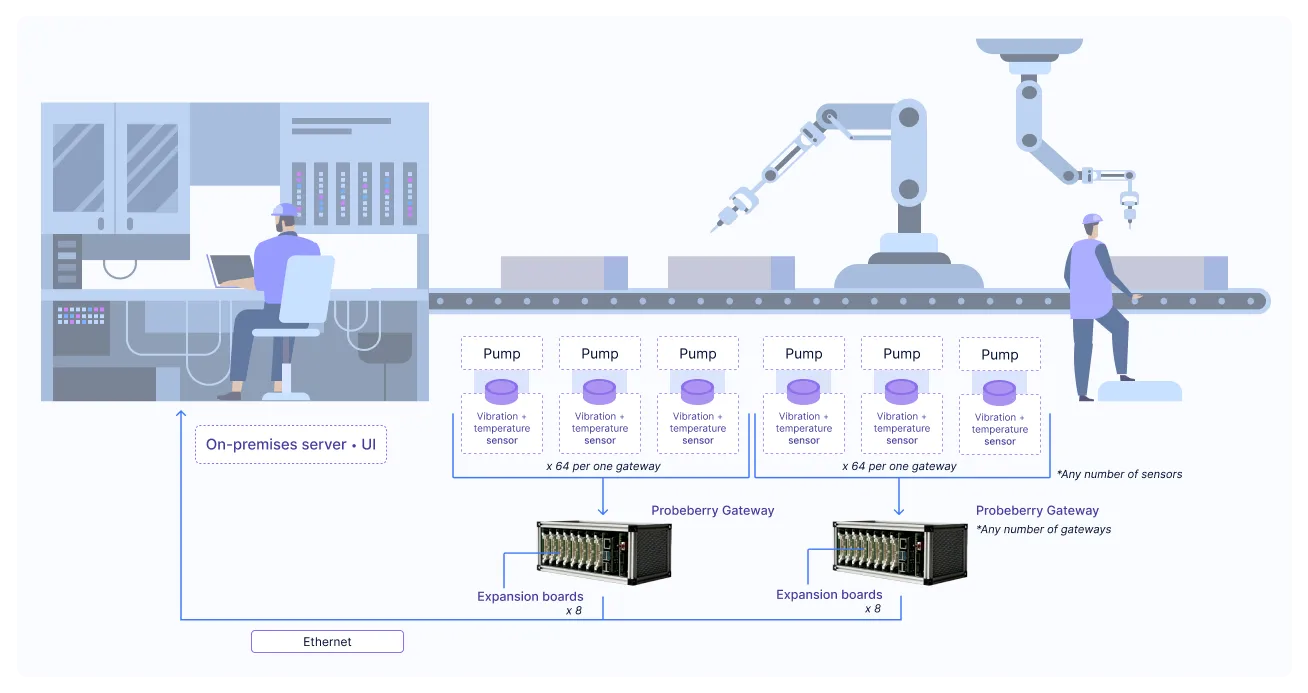
Therefore, the customer was offered an inclusive out-of-the box solution consisting of fully customized modules.
The final delivery kit included:
- 14 Ethernet gateways
- On-premises server
- User interface
04
Current status of the project
The solution was successfully implemented in the customer's PCB manufacturing facilities in March 2023.
.webp)
05
Benefits of the implemented monitoring system
Assistance from start to finish
Our team stay in close contact with the customer during the whole project, from defining the main goal and throughout the system installation in the factory. While most of the installation work can only be performed by the authorized personnel from the customer’s side, our representatives are entrusted to install the on-premises server and run the functional tests on-site.
On-premises deployment
The designed solution allows storing the received data and maintaining the hardware in-house. To have more control over security, performance, data, and access, the majority of production facilities use a local network. The Prylada can equally provide solutions for both cloud and on-premises deployment.
Full customization
The Prylada team considered multiple factors to figure out the best suitable solution, which would create additional value to the customer’s business by optimizing the PCB manufacturing processes. All the components, from sensors to user interface, are tailored to fulfill the defined needs.
Automate your physical asset monitoring to bring additional value to your business
Get in touch06
FAQ
Vibration monitoring is a process of measuring vibration level of equipment to recognize any anomalies in the equipment health.
Vibration monitoring solutions measure vibration level of equipment by special sensors, such as probes, accelerometers, transmitters, and switches. These sensors record the frequency and amplitude of the vibration signature of a machine. Then the received measurements are compared with the standard or recommended levels to detect potential issues with the equipment
When an abnormality occurs in the operation of a machine, its vibration signature changes. In manufacturing, abnormal vibration typically indicates defects, breakdowns, or failures inside the equipment (especially in rotating machines like pumps, motors, turbines, fans, and compressors) and can thus be used to diagnose problems.
Here is the list of the common machinery problems that cause vibration from our tech team.
• Misalignment of couplings, bearings and gears
• Unbalance of rotating components
• Looseness
• Deterioration of rolling-element bearings
• Gear wear
• Rubbing
• Aerodynamic/hydraulic problems in fans, blowers and pumps
• Electrical problems (unbalance magnetic forces) in motors
• Resonance
• Eccentricity of rotating components such as “V” belt pulleys or gears