Probeberry Gateway
Designed to collect data from sensors, process it, react according to predefined scenarios, and communicate with a remote control center running on a cloud or an on-premises server.
Request a demo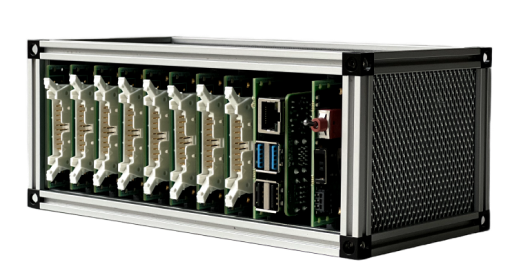
Operating principle
The Probeberry Gateway is a modular signal processing system built around Raspberry PI. Raspberry PI controls up to 8 I/O modules receiving/sending input/output data in real-time. Every module reads data from multiple sensors, connected directly or via a bus, or it controls devices, either connected directly to the gateway or receiving setpoints via a serial bus or wireless network.
The data collected from the sensors can then be sent to the Prylada Cloud, a private cloud, or an on-premises server, depending on your business requirements. In turn, the server upon the received data analysis can react by sending commands to the gateway according to predefined scenarios.
.webp)
%20(1).webp)
Every I/O module can be one of more than 10 types: complex 8-channel analog input/output, relays, analog multiplexor, RF, software controlled power supplies, industrial serial buses, etc.
Whatever solution is applied–the Prylada Cloud or an on-premises server–a customer can equally use the same set of features, starting from the remote gateway configuration and finishing with control scenarios development and received data visualization on intuitive widgets.
Features
- Open, modular architecture. Customers can develop their own modules for the gateway.
- Replaceable power supply module. The default 90W version works in the range 18-26 DC and provides gateway with 3.3V/6A max and 15V/6A max.
- Raspberry PI is connected to the system via an expansion board. In the same way Arduino or other controllers can be connected.
- Up to 8 expansion modules are supported.
- Sensors/devices can be connected in any way, directly to the analog/digital inputs/outputs or via various buses–MODBUS, SMBUS, SDI, RF, WI-SUN, etc.
- Various deployment options–Prylada cloud, private clour,
on-premises server - Third-party test frameworks like Coronys Center, etc.
- Third-party modeling software
- API–provided to enable connection to the various process
automation or data management systems
- Open, modular architecture. Customers can develop their own modules for the gateway.
- Replaceable power supply module. The default 90W version works in the range 18-26 DC and provides gateway with 3.3V/6A max and 15V/6A max.
- Raspberry PI is connected to the system via an expansion board. In the same way Arduino or other controllers can be connected.
- Up to 8 expansion modules are supported.
- Sensors/devices can be connected in any way, directly to the analog/digital inputs/outputs or via various buses–MODBUS, SMBUS, SDI, RF, WI-SUN, etc.
- Various deployment options–Prylada cloud, private clour,
on-premises server - Third-party test frameworks like Coronys Center, etc.
- Third-party modeling software
- API–provided to enable connection to the various process
automation or data management systems
Learn how to automate vibration monitoring in PCB manufacturing with the Probeberry Gateway
Read moreAvailable connectivity
Analog/digital input/output
Up to 8 isolated on-the-fly software programmable inputs/outputs per module
Interfaces
I2C RS232 RS485
Sub-1GHz RF
Wi-SUN® protocol support
Analog multiplexer
4 analog multiplexers 1:4
Ask for module specifications
Leave us your email, and we will reach out to you to provide with all the necessary information
Application
The Probeberry Gateway can be used to automate control of physical infrastructure and optimize data management at various manufacturing facilities and laboratories. By transferring data from sensors/devices to a remote control center in real-time, you can get the full picture of the current workflow and observe the condition of your equipment. This in turn helps you enable predictive maintenance of the critical assets and reduce operational costs.
By setting specific control scenarios, you can program the gateway to operate as a controller and automatically coordinate the production processes.
The capability to switch between the battery power and AC power allows the gateway to work in full absence of external power source and ensure uninterrupted operation in case of emergency.
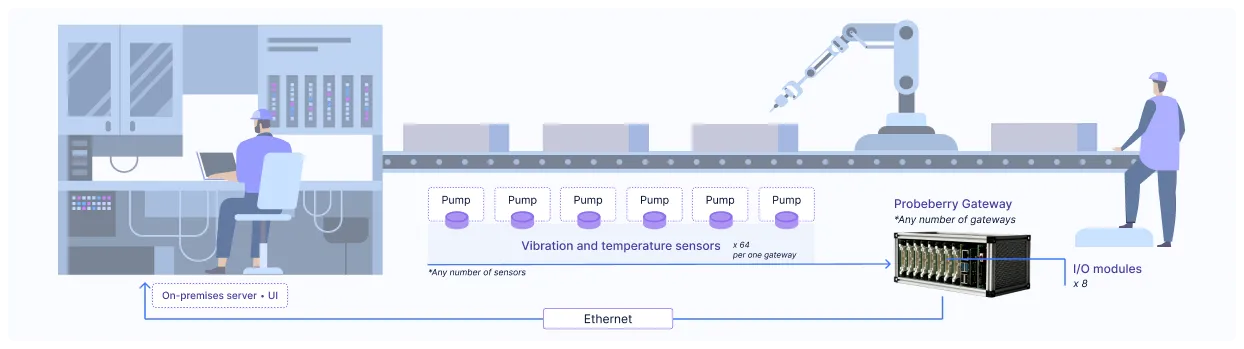
%20(2).webp)